Biocompatible ISO Certified Medical Coating
Greystone have used 90 years of experience to create the coating designed for the medical market: a biocompatible STERIChrome™ layer. STERIChrome™ coating drastically improves both the physical appearance and performance of your product. This proprietary process for plating is an industry-leading application for durable, antimicrobial, wear-resistant and corrosion-proof device coatings. STERIChrome™ is a highly customizable, scientifically tested, ISO-approved precision coating used in Medicine.
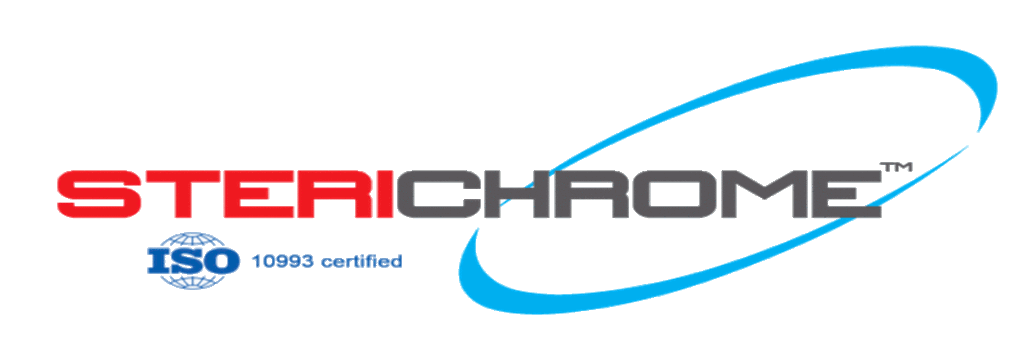
STERIChrome™: Certified to ISO 10993.
Our clients are ensured, that STERIChrome™ have:
- Maximum repellent against blood, urine, saliva and other bio-fluids.
- Increased self-cleaning, antifouling and anti-corrosion properties
- Reduced risk of contamination and patient infection
- Long lasting and improved durability
STERIChrome™: Fluid Repelling layer.
When it comes to safety-critical medical and dental device components, moisture can present a challenge. Instrument spotting, staining and corrosion are common in healthcare facilities due to autoclave procedures and sterile processing. This will impair instrument function and interfere with future sterilization procedures. With our hydrophobic coatings, our clients are assured that instrument function will be maintained.
STERIChrome™ specification includes:
- Surface Hardness: 72-80+ HRC
- Thickness Range: 1,27µ - 50,8µ (0.000050"-0.002")
- Thickness Control: 2,54µ (0.0001")
- ISO 13485 approved and Biocompatibility Certified to ISO 10993
- Reflective & Matte finishes available
STERIChrome™: Durable Coating.
STERIChrome™ is ideal for a durable and corrosion resistant for high-friction applications.
We work with our global clients to precisely electroplate medical and dental tools, such as:
- Endoscopic instruments and cutters
- Powered hand instruments
- Orthopedic instruments and tooling
- Valves, handles, housings and tubing
- Dental hand instruments and reamers
- Surgical saws, taps and drills
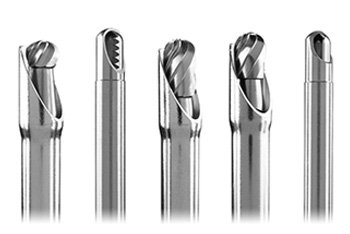
STERIChrome™ advantages:
surface hardness significantly improves instrument wear and abrasion resistance to eliminate galling and fretting
maximizes blade integrity to maintain cutting edges
prevents corrosion as a result of sterile processing and laser marking
no metallic debris during operation
finish gives instruments long-lasting color and reduces high intensity light reflection